Eirichmischer in ATEX-Ausführung bei Reibbelagherstellern sehr gefragt
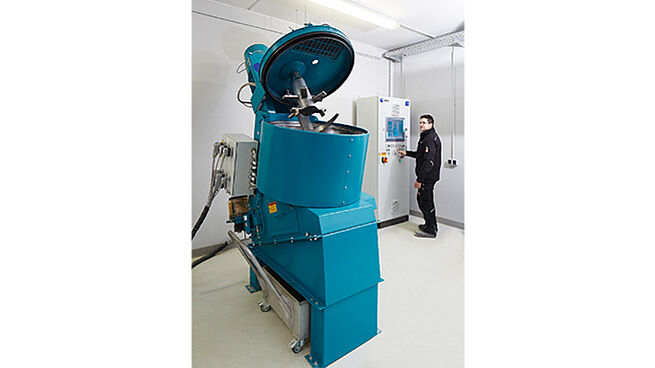
Reibbelägen in Form von Brems- und Kupplungsbelägen auf organischer Bindemittelbasis kommt eine große Bedeutung zu. Bewegungsenergie wird durch Reibung in Wärme umgewandelt. Der Reibbelag muss eine gleichbleibende Reibung aufweisen. Druckfestigkeit, Scherfestigkeit und Werkstoffhärte dürfen über den ganzen Belag keine Schwankungen aufweisen. Bei den Mischungen, die zu Reibbelägen verpresst werden, bestehen aus diesem Grunde hohe Anforderungen an die Homogenität. Namhafte Hersteller setzen deshalb auf die beste verfügbare Mischtechnik. Diese ermöglicht es zudem, Trocken- und Nassmischungen in ein und derselben Maschine aufzubereiten. Auch in 2020 hat EIRICH wieder mehrere Mischer projektiert, unter anderem für Hersteller in Süd- und Osteuropa. Dabei wurden nahezu alle Mischer ATEX-konform ausgeführt, wie in dieser Branche fast immer Standard.
Reibbeläge bestehen aus einer Vielzahl von Rohstoffen, bis zu 50 in einer Rezeptur. Die Stoffe weisen extrem unterschiedliche Schüttgewichte auf, von rund 50-100 g/l bei Fasern bis über 4.000 g/l bei metallischen Bestandteilen. Dies stellt hohe Anforderungen an die Mischtechnik.
Die Rezepturen der Hersteller sind entwickelt und abgestimmt auf die jeweilige Anwendung bzw. auf die Anforderungen von Kunden. Inhaltsstoffe sind anorganische Füllstoffe, Schmierstoffe sowie Metalle als Pulver, Körnung oder Fasern. Oft kommen auch Kunststofffasern - beispielsweise auf Basis von Aramiden - zum Einsatz, die bei Hitzeeinwirkung nicht schmelzen, sondern verkoken. Dazu kommt das bindende Harz, das im Ablauf der Produktion unter Wärmeeinwirkung verkokt und alle Partikel miteinander verbindet. Neue Bindungssysteme auf Basis Graphit, die unter Druck eine mechanische Bindung ergeben, arbeiten harzarm oder harzfrei.
Bei allen Rezepturen müssen sehr leichte Stoffe mit sehr dichten Stoffen sowie Fasern optimal gemischt werden – für den Mischer eine echte Herausforderung, zumal die Fasern oft aufgeschlossen werden müssen. Literaturbekannt ist, dass „normale“ Mischer beim Mischen entmischen, weil dem Vermischungsprozess ein Entmischungsprozess überlagert ist. Insbesondere bei Mischungen mit verschieden dichten Rohstoffen kommt dies zum Tragen. So ergaben Untersuchungen zur „Mischzeitbestimmung an einem horizontalen Einwellenmischer“ (Typ Pflugscharmischer) mit zwei Testsubstanzen, dass man nur 120 Sekunden mischen darf. Mischt man länger, treten Entmischungserscheinungen der beiden Komponenten ein. Erklärt wird dies durch das unterschiedliche Bewegungsverhalten der Komponenten im Mischer; in der Folge kommt es zu einer allmählichen Anreicherung der schweren Komponenten in den Randbereichen.
Dies bedeutet in der Praxis, dass man in solchen Mischern nicht beliebig lange mischen darf und mit Messreihen die Mischzeit für die jeweils besterreichbare Mischgüte ermitteln muss, die meist nicht die optimale Mischgüte ist. Diese Erkenntnisse gelten für alle Mischer, bei denen der Mischguttransport durch Mischwerkzeuge erfolgt. Entmischte, also inhomogene Pressmasse führt zu Streuungen in der Qualität und möglichen Problemen beim späteren Einsatz.
Um optimale Mischgüten zu erreichen und ohne Entmischen zu mischen, entscheiden sich Hersteller von Reibbelägen regelmäßig für die Eirich-Mischtechnik. Hier erfolgt der Transport des Mischgutes nicht durch Mischwerkzeuge, sondern durch einen drehenden Behälter. Dieser Mischer kommt in einer Vielzahl von Branchen immer dann zum Einsatz, wenn andere Mischsysteme systembedingt ihre Grenzen erreichen. Viele Untersuchungen zeigen, dass damit Mischgüten erreichbar sind, die in der Regel von anderen Systemen nicht angefahren werden können. Das Wirkprinzip mit drehendem Mischbehälter und Materialumlenker verhindert, dass schlecht durchmischte Totraumzonen im Mischer entstehen, da jedes Teilvolumen des Mischgutes dem Wirblerwerkzeug zugeführt wird. Auch das Auftreten einer Entmischung im Mischer wird damit zuverlässig ausgeschlossen.
Weil Materialtransport (durch den drehenden Behälter) und Mischen (durch das Mischwerkzeug, Wirbler genannt) voneinander getrennt sind, kann das Mischwerkzeug beliebig schnell laufen, mit Werkzeuggeschwindigkeiten bis zu 30 m/s, je nach Prozessschritt. Deshalb braucht dieser Mischer zum Aufschließen von Fasern keine schnelllaufenden und verschleißintensiven Messerköpfe. Und es sind Froudezahlen erreichbar, die beim Mehrfachen dessen liegen, was bei anderen Mischsystemen machbar ist. Die Folge ist, dass der Eirichmischer beliebige Konsistenzen verarbeiten kann. Bei Reibbelägen sind es in der Regel Trockenmischungen oder Mischungen mit Harzlösungen – für den Mischer kein Problem. Beide Mischungen können auf ein und derselben Maschine hergestellt werden. Selbst zähflüssige Harzlösungen werden problemlos verarbeitet, was bei herkömmlichen Mischern nur sehr schwer oder gar nicht möglich ist. Und natürlich sind auch Reibbeläge der neuen Generation auf Basis von Graphit damit bestmöglich aufzubereiten.
Kunden – darunter die renommierten Reibbelag-Hersteller in aller Welt – schätzen bei den Mischern auch den systembedingt niedrigen Verschleiß und die vergleichsweise leichte Reinigbarkeit. Dies ist für sie regelmäßig ein weiterer Grund, auch bei Produktionserweiterungen der Eirich-Technik treu zu bleiben. Meist kommen Mischer zwischen 75 und 1.500 Liter Nutzvolumen zum Einsatz, in der Regel mit ATEX-Ausrüstung. Systembedingt ist auch das Upscaling relativ einfach. Dies ermöglicht es, auf einfache Weise Rezepturen von kleinvolumigen Versuchsmischungen auf große Produktionsmischer zu übertragen.
Je nach Anforderung werden die Mischer explosionsgeschützt (innen bei Nassaufbereitung Zone 21, bei Trockenaufbereitung Zone 20, außen Zone 22) ausgeführt, entsprechend den europäischen ATEX-Vorschriften. Bei Bedarf erfolgt auch die Auslegung für die Gasexplosionsschutz-Zonen 0, 1 oder 2. Die Mischer können bei Bedarf auch mit induktiver Beheizung ausgestattet werden, die selbstverständlich ATEX-konform geliefert wird.
An allen Eirich-Standorten weltweit stehen Technikumseinrichtungen bereit, in denen die systembedingten Vorteile der besonderen Mischtechnik mit den Rohstoffen des Kunden vorgeführt werden können. Im Vergleich zu anderen Mischern ergeben sich meist deutlich kürzere Mischzeiten, was den Einsatz kleinerer Mischer ermöglicht, und das bei besserer Reproduzierbarkeit.
Weitere Informationen:
Ansprechpartner: Oliver Zeitner, E-Mail: oliver.zeitner@eirich.de