EIRICH verzeichnet zunehmende Nachfrage nach Mischern für Faserbetone
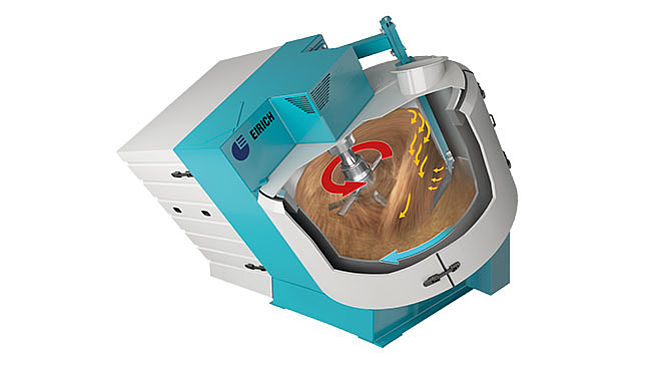
Für viele Anwendungen werden Betonen Fasern zugesetzt, insbesondere zur Verbesserung des Riss- und Bruchverhaltens. Die Sprödigkeit der Betonmatrix nimmt durch Faserbeimischung ab, der Beton wird dadurch verformbarer und kann Biegebeanspruchungen besser widerstehen. Je nach Verwendung werden Stahlfasern, Glasfasern oder Kunststofffasern eingesetzt, letztere auch zum Brandschutz, insbesondere beim Tunnelbau. Kommt es zu einem Feuer, verbrennen die Fasern und hinterlassen Kanäle, durch die Wasserdampf entweichen kann. Damit kann verhindert werden, dass die Randschicht des Betonbauteils abplatzt; die dahinter liegende Stahlbewehrung bleibt geschützt. Zu fordern ist, dass die Fasern im Beton gleichmäßig verteilt sind. Dies stellt hohe Anforderungen an die Mischtechnik zum Anmachen des Betons. Auch hier bewährt sich die Mischtechnik von Eirich.
Faserbeton ist ein relativ junger Werkstoff, um 1970 wurden ein erstes Mal Stahlfasern eingesetzt, Glas- und Kunststofffasern folgten. Als die Mischer für Betone erfunden wurden, gab es noch keine Faserzusätze. Die heutigen Ausführungsformen der Mischer, meist nahezu baugleich von vielen Herstellern weltweit angeboten, ähneln stark denen der Originale vor mehr als hundert Jahren: Der Einwellenmischer (um 1870), der Doppelwellenmischer (1888), der Ringtrogmischer (um 1903) und der Planetenmischer (1906). Aus dem Planetenmischer wurde 1924 der Eirichmischer mit waagrecht stehendem Mischbehälter entwickelt, 1972 erfolgte die Weiterentwickung zum Mischer mit schräg stehendem Mischbehälter. Im Unterschied zum Planetenmischer hat der Eirichmischer einen sich um eine vertikale Achse drehenden Mischbehälter und ein exzentrisch angeordnetes Mischwerkzeug.
Den Mischern, die auf Erfindungen zwischen 1870 bis 1906 zurückgehen, ist eigen, dass die Mischwerkzeuge im Mischbehälter boden- bzw. wandnah laufen. Die Mischwerkzeuge transportieren das Mischgut, auch Randbereiche müssen erfasst werden. Insbesondere um reibungsbedingten Verschleiß in Grenzen zu halten, liegen die Werkzeuggeschwindigkeiten niedrig, oft bei nur 1,5 m/s.
Beim Eirichmischer übernimmt ein drehender Behälter den Transport des Mischgutes. Dieses wird dem Mischwerkzeug, Wirbler genannt, zugeführt. In Baugrößen von 1 Liter bis 3000 Liter wird nur ein einziges Wirblerwerkzeug benötigt. Erst in größeren Mischern werden mehrere Wirbler eingebaut, z. B. bei 12 m³ Nutzfüllung 4 Wirbler.
Charakteristisch für dieses Mischsystem ist, dass der Wirbler nur zwei kleine, berührungsfrei arbeitende Bodenabreinigungsmesser braucht, um den Boden des Mischbehälters ansatzfrei zu halten. Die Verlustleistung über Reibung und damit auch der Verschleiß des Bodens sind deshalb sehr gering (weshalb Eirichmischer auch keine Keramikauskleidungen brauchen). Dies ermöglicht auch hohe Werkzeuggeschwindigkeiten, mit entsprechend hohem Leistungseintrag. Der Wirbler kann – falls für die jeweilige Aufgabe erforderlich – mit Werkzeuggeschwindigkeiten von bis zu 30 m/s laufen. Es versteht sich von selbst, dass zugesetzte Fasern – gleichgültig ob Kurz- oder Langfasern - bei höheren Werkzeuggeschwindigkeiten leichter vereinzelt und verteilt werden können, und einer Klumpenbildung – im Fachjargon Igel-Bildung genannt - vorgebeugt werden kann. Dabei kann innerhalb einer Charge mit mehreren verschiedenen Geschwindigkeiten gearbeitet werden und so für jeden Aufbereitungsschritt des Mischregimes die optimale Geschwindigkeit und damit der passende Leistungseintrag gewählt werden.
Dazu kommt: Jedem Mischvorgang ist ein Entmischvorgang überlagert, im Wesentlichen bewirkt durch Zentrifugalkräfte, insbesondere wenn die Komponenten des Mischguts – wie bei Betonen – unterschiedliche Dichten und Korngrößen aufweisen. Untersuchungen an Betonmischern gab es dazu schon um 1980, mit dem Ergebnis: Man darf nicht beliebig lange mischen, weil die Mischgüte dann wieder abnimmt. Dies ist auch der Grund, warum Betonnormen nicht vorgeben, „gut“ zu mischen, sondern nur, bis die Mischung gleichförmig erscheint. Es ist deshalb oft nicht möglich, das Optimum der Mischgüte anzufahren.
Beim Eirichmischer ergibt sich hingegen während einer einzigen Umdrehung des Behälters eine vollständige Durchmischung. Das beim Wurfvorgang vom Wirbler lokal entmischte Produkt wird durch die permanente Umwälzbewegung wieder rückvermischt, der Mischer mischt deshalb ohne Entmischen. Man kann in der Folge damit so lange mischen, wie die jeweilige Aufgabenstellung es erfordert.
Viele Hersteller von Betonfertigteilen nutzen heute die beste verfügbare Technik – die Mischtechnik von Eirich. Anzumerken ist, dass man bei Faserbeton den Begriff Beton auch dann benutzt, wenn das Größtkorn kleiner als 4 mm ist. Solche Faserbetone sind in Bezug auf die Mischtechnik besonders anspruchsvoll. Auch die Glasfaserbetonplatten für die Fassade des Stadion Johannesburg, das für die Fußball-Weltmeisterschaft 2010 errichtet wurde, wurden mit Eirich-Mischtechnik hergestellt. Die Gestaltung der Fassade sollte an ein traditionelles afrikanisches Trinkgefäß erinnern. Die 40.000 Glasfaserbetonplatten in verschiedenen afrikanischen Farben lieferte das österreichische Unternehmen Rieder Smart Elements mit Produktionsstandort in Kolbermoor, nahe Rosenheim, Oberbayern.
Eirich erreichen in letzter Zeit regelmäßig Anfragen von Fertigteilherstellern, die qualitativ hochwertigen und gleichmäßigen (Faser-) Beton herstellen wollen. Dabei interessiert neben der Mischtechnik auch die vollautomatische Faserdosierung für Klein- und Großmengen, für die Eirich bewährte Lösungen anbieten kann.
Weitere Informationen:
Ansprechpartner: Stefan Berberich, E-Mail: stefan.berberich@eirich.de